USE CASE 1 : Project Overview
In bearing manufacturing, defect-free parts hold the utmost importance. A traditional inspection method is both slow and error-prone with a tendency to miss defects as small as possible. Therefore, an AI-based vision inspection system was put forward to improve the quality of defect detection and identification in this regard.
The process of inspecting bearing parts is cumbersome and inaccurate. Sometimes, it fails to detect all defects, which would compromise the quality of products and increase cost. A more advanced solution is therefore required to automate and enhance the inspection process.
Solution Proposed:
This was a tailored AI-based vision inspection system for real-time inspection of bearing parts. The system used high resolution cameras with machine learning algorithms to inspect the parts against defects and classify them as either accept or reject. Additionally, it provided analytics for the collected inspection data, which improved the throughput and manufacturing efficiency.
Impact
The AI-based vision inspection system provided
- Improved detection accuracy: Improved accuracy in detection and classification of defects.
- Improved throughput: Automated inspection enables faster production cycles.
- Data-driven insights: Continuous data analytics for better process refinement.
With this advanced AI solution, the bearing manufacturer achieved better quality control standards, reduced operational costs, and overall improved production efficiency.
USE CASE 2 : Project Overview
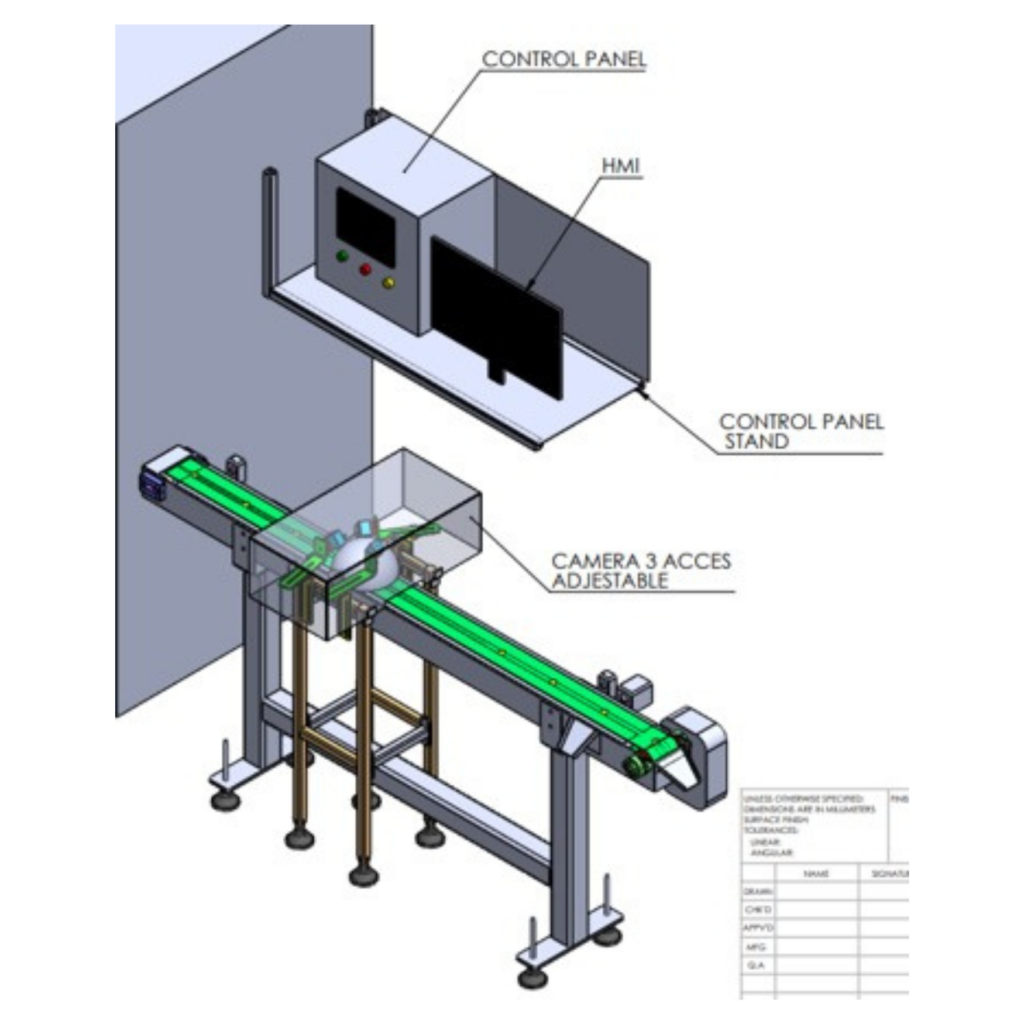
The manufacturing of bearings requires that parts be defect-free. Manual inspection methods are time-consuming and susceptible to human error, missing critical defects such as cracks and chip marks. An AI-based vision inspection system was proposed to enhance the detection and identification of defects.
Problem Statement:
The manual inspection process for bearing parts is inefficient and fails to detect all types of defects. This leads to a reduction in product quality and an increase in costs. A more advanced solution was needed to automate and improve the inspection process for better accuracy and efficiency.
Solution Proposed:
This would implement an in-house, customized AI-based vision inspection system that employed high-resolution cameras and applied machine learning algorithms to check bearing parts in real time for defects such as cracks and chip marks, classify these defects, and conduct exhaustive data analytics.
Impact:
- Enhanced Detection Accuracy: Achieving higher precision in detecting and classifying defects.
- Increased Efficiency: Reducing inspection time and allowing faster production cycles.
- Data-Driven Insights: Continuously providing data analytics to help refine the process and enhance quality control.
The incorporation of this advanced AI solution helped the bearing manufacturer realize higher quality standards, lower operational costs, and increased overall production efficiency.